Yüksek manganlı çelik döküm parçalarda çatlakların yapısı
Bu yazıda çelik döküm parçalarda gördüğümüz çatlakların yapısı üzerinde duracağız. Bu çatlakların yapısına odaklanmaktaki amacımız
Çatlakların oluşması sadece tek bir işleyişe bağlı değil. Farklı çelik türlerinde ya da farklı özelliklere sahip parçalarda karşılaştığımız çatlaklar, farklı farklı nedenlerle ortaya çıkabiliyorlar. İşin kötü tarafı ise, bu çatlakları haliyle iş işten geçtikten sonra, yani parçayı kalıptan çıkardıktan sonra görebiliyoruz. Döküm simülasyon programları bu noktada dökümcülere bir yere kadar yardımcı olabiliyor. Bu çatlaklar çoğu zaman kalıp içindeki parçanın homojen bir şekilde soğumuyor olması nedeniyle oluştukları için, bu yazılımlar yardımıyla bu çatlaklardan bir yere kadar kaçınmanıza olanak sağlayacak şekilde kalıp tasarımlarınızı gözden geçirebiliyorsunuz. Fakat işin içine kimyasal kompozisyona bağlı nedenlerle oluşan çatlaklar girdiği zaman, o zaman iş ister istemez kontol altına alınmasıa daha zor bir hale geliyor.
Manganlı çelik
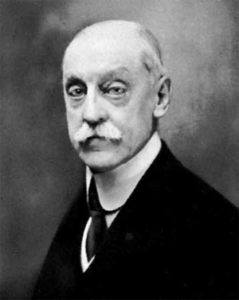
Manganlı çeliği 1882 senesinde geliştiren İngiliz metalurjist Sir Robert Hadfield (Kaynak: Britannica).
Kimyasal kompozisyondan bahsetmeye başladığımız bu noktada, bu yazının esas konusu olan yüksek manganlı çelikler hakkında kısa bir bilgi vermemiz yerinde olacaktır. Bu alaşım, farklı kaynaklarda farklı isimlerle anılabiliyor: Örneğin bazı kaynaklarda manganlı çeliklerden Hadfield çeliği ya da Mangalloy adıyla bahsedildiğini görmüş olabilirsiniz.
Bu alaşımı işin kitabına sadık kalarak tarif etmek istersek, yaklaşık %0,8 ile %1,25 arasında karbon, %11 ile %15 arasında mangan içeren bir çelik alaşımı olduğunu söyleyebiliriz. Genelde malzemelerin sertiği arttıkça aşınma dirençlerinin arttığını, fakat tokluklarının azaldığını görürüz. Manganlı çelikler ise deformasyon sertleşmesi sonrasında aşınmaya karşı oldukça dayanıklı bir yapıya geçmelerine rağmen, aynı zamanda darbeye karşı yüksek bir dayanım da sergiliyorlar. Yani, tokluklarını kaybetmiyorlar.
Bu kabiliyet nasıl ortaya çıkıyor? İşin sırrı malzemenin yapısında saklı: Dökümhanelerde dökülen çelik parçalara baktığımızda, ortalama bir değer vermek gerekirse, genellikle bu parçaların %0,15 ile %0,8 arasında mangan içerdiklerini görüyoruz. Yüksek dayanıma sahip çeliklerde mangan miktarı en fazla %1,5 civarına kadar arttırılabiliyor. Çünkü mangan miktarı daha arttığı zaman, çelik kırılganlaşmaya başlıyor.
O zaman bu kadar yüksek manganın çelikte işi ne? Yukarıda da dediğimiz gibi, işin sırrı malzemenin yapısında saklı: Parçayı doğru bir şekilde soğutabilmişsek, %10’un üzerine eklenen mangan, yüksek sıcaklıkta kararlı olan östenit fazının, ferrit ve perlite dönüşmesini engelliyor. Yani 723°C civarında ortadan kalkması gereken östenit fazının, parça oda sıcaklığına soğuduğunda bile malzemenin yapısında bulunduğunu görüyoruz. Bunun sonucu olarak malzeme bir yandan sertleşirken, bir yandan da sünekliğini koruyor: Yani hem aşınma direncine, hem de nispeten yüksek bir tokluğa sahip oluyor.
Parçalar neden çatlıyor?
Yüksek manganlı çeliklerin katılaşma sırasında çatlayabildiklerini biliyoruz. Peki bu çatlaklar hangi aşamada oluşuyor? Çatlakların oluşabilmesi için parçanın katılaşmaya başlamasının gerektiği açık: Bugüne kadar sıvı içinde çatlak oluştuğunu gören yoktur herhalde.
Fakat işin püf noktası şurada: Çatlak oluşması için parçanın tamamen katılaşmasına gerek yok. Kısmi katılaşmış parçalar, aslında çatlak oluşumuna çok ciddi şekilde meyilli olabiliyorlar. Kısmi katılaşmış derken (yandaki resimde görüldüğü gibi) katılaşmış tanelerin, sıvıyla birlikte bulunduğu durumu kastediyoruz. Böyle yarı katılaşmış bir parça içinde farklı soğuma hızları oluşunca ister istemez ortaya gerinimler de çıkıyor. Taneleri arada tutan bir şey olmadığı için (taneler arasında ince sıvı filmleri olduğuna dikkat ediniz), bu gerinime dayanamayan taneler ayrılıyor. Bunun sonucu olarak sıcak yırtılma dediğimiz, tanelerin yüzeylerini ortaya çıkartan gevrek kırılma gerçekleşmiş oluyor.
Buraya kadar güzel. Şimdi bu noktada bir şeyi açıklığa kavuşturalım:Eğer kırılma, camın çatlaması gibi, gevrek bir şekilde olmuşsa, o zaman parlak ve düz bir kırılma yüzeyi görürüz. Fakat eğer parça sünek bir şekilde kırılırsa, o zaman ortaya mat ve pürüzlü bir kırılma yüzeyi çıkar. Çünkü çatlama sırasında bir miktar deformasyon da gerçekleşmiştir.
Bizim yukarıda açıkladığımız kırılma mekanizması, tanelerin parlak yüzeyini ortaya çıkartan gevrek kırılma işleyişi. Peki çelik parçalarda sadece bu mekanizma mı gerçekleşebilir, diye soracak olursanız, bunun cevabı hayır. Sıcaklığa bağlı olarak hem gevrek, hem de sünek kırılma ortaya çıkabiliyor. Örneğin Polonyalı araştırmacıların gerçekleştirdiği ve sonuçları alttaki resimde verilen çalışmada, manganlı çelikler 1275°C’de test edildiği zaman geride pürüzsüz tane yüzeyleri bırakan gevrek kırılma gerçekleştirken, 1131°C’de yapılan testlerde pürüzlü ve mat yüzeylere yol açan sünek kırılmanın ortaya çıktığı görülmüş (çalışmanın ayrıntıları resmin altında verilmiştir).
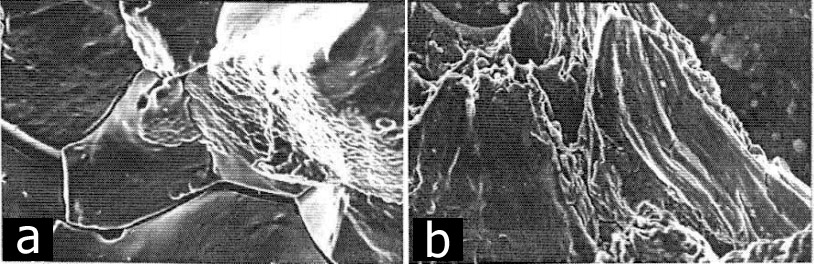
(a) 1275°C’de taneler arasında ilerleyen çatlak gevrek kırılmaya işaret ediyor, (b) 1131°C’de görülen sünek kırılma (Kaynak: A. Chojecki, I. Telejko. Cracks in high-manganese cast steel. Archieves of Foundry Engineering, Vol 9 (2009) 17-22)
Bu iki mekanizmanın farklı şekillerde gerçekleşmesine yol açan şey, sıcaklık. Daha doğrusu, çatlamanın solidus sıcaklığının altında ya da üstünde gerçekleşmiş olması.
Daha yalın bir dille ifade etmeye çalışalım: Yukarıda (a) ile gösterilen gevrek kırılma durumunda, çatlak oluştuğu sırada parça tam anlamıyla katılaşmış durumda değil. Taneler arasındaki sıvı film taneleri bir arada tutamadığı için, tanelerin resimde gösterildiği gibi birbirlerinden ayrıldıklarını görüyoruz. Sağda (b) ile gösterilen durumda ise solidus sıcaklığının altındayız. Dolayısıyla artık ortada sıvı film falan yok, parça tamamen katılaşmış durumda. Fakat soğuma hızına bağlı gerilimler nedeniyle, özellikle ufak çekintilerin (boşlukların) etrafında gerinim yoğunlaşarak parçanın deforme olmasına, ve bunun sonucu olarak da resimde görüldüğü şekilde sünek bir işleyişle kırılmasına yol açıyor.
Bu noktada, bu sünek kırılma işleyişinin açığa çıkması için malzeme yapısında mutlaka çekintiler olması gerektiğini de vurgulayalım. Yapılan çalışmada, bu çatlakların daima çekintiler etrafından büyümesi sonucunda sünek kırılma yapısının ortaya çıktığı vurgulanıyor. Dolayısıyla, eğer döktüğünüz parçada böyle sünek yapı sergileyen çatlaklar görüyorsanız, çatlaklardan ziyade aslında sizin çekinti problemi yaşadığınızı söyleyebiliriz.
Kimyasal kompozisyonun etkisi
Sıcak yırtılmadan bahsederken, kimyasal kompozisyonun etkisini de mutlaka dikkate almamız lazım. Çeliğin kompozsiyonunda karbon, silisyum ve mangan oranlarının yüksek olması, taneler arasında segregasyonu teşvik ederek, geride kalan sıvının donma sıcaklığının 900°C civarına kadar düşmesine yol açabiliyor. Taneler arasında biriken fosfor ve karbonun yüksek seviyede olması sonucunda, tane sınırlarında fosfor ve karbür ötektiklerinin oluştuğunu görebiliyoruz. Bir ağ gibi tane sınırlarını kaplayan bu fazlar kırılgan bir yapıya sahip olduğu için, katılaşma sırasında çatlayarak gevrek kırılmanın başlamasına yol açabiliyorlar.
Elbette bu yazıda üzerinde durmadığımız ve sıcak yırtılma sürecine etki edebilecek farklı faktörlerden de bahsedebilir, ya da konunun daha da ayrıntılarına girebiliriz. Fakat hem basit bir giriş yapmak, hem de yazıyı daha fazla uzatmamak adına şimdilik bu mekanizma hakkında bu kadar bilgi vermekle yetineceğiz. O nedenle şimdilik konunun ince ayrıntılarını, çelik dökümü üzerine kaleme alacağımız diğer yazılara bırakacağımızı söylemekle yetinelim.
Kaynaklar ve ek bilgiler
İçerik hazırlığında kullanılan tüm kaynakların listesi için bu bağlantıyı takip edebilirsiniz.
Yazan: Dr. Arda Çetin. (Dökümhane Akademi ekibi hakkında ayrıntılı bilgi için bu bağlantıyı takip edebilirsiniz.)