Yüksek alaşımlı beyaz dökme demirler
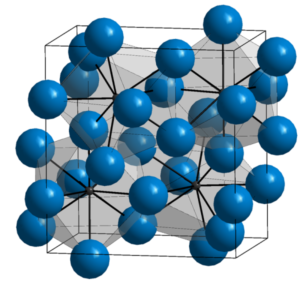
Sementit fazının kristal yapısı. Demir atomları mavi, karbon atomları (küçük) ise siyah renkle gösteriliyor. Kaynak: Wikimedia Commons (CC BY-SA 3.0)
Bu yazıda, önceki haftalarda nispeten ihmal ettiğimiz yüksek alaşımlı beyaz dökme demir türleri üzerinde duracağız. Beyaz dökme demirin yapısına aşina olmayan ve ayrıntılı bilgi isteyen okurlarımız, daha önce yayımlanan bu yazıdan bilgi alabilirler. Fakat bu uzun yazı için zamanı olmayan ve kısa bir özetin yeterli olacağını düşünen okurlarımız için, beyaz dökme demirlerde karbonun grafit halinde ayrışmadığını ve tıpkı çeliklerde olduğu gibi yapıda çözünmüş durumda kaldığını söyleyerek başlayabiliriz. Grafit ayrışması gerçekleşemediği için, beyaz dökme demirlerde karbon atomlarının, sementit adı da verilen demir karbür parçacıkları içinde yer aldıklarını görüyoruz. Oldukça sert bir yapı sergileyen sementit fazı nedeniyle beyaz dökme demirler, yüksek aşınma direnci istenen uygulamalarda öne çıkıyor.
Yüksek alaşımlı beyaz dökme demirler
Yüksek alaşımlı beyaz dökme demirlerin ardındaki temel düşünce, zaten yüksek aşınma direncine sahip olan beyaz dökme demirlerin aşınma direncini daha da arttırmak. Sıradan bir beyaz dökme demir alaşımı yaklaşık 350 – 550 HB aralığında sertlik değerleri verirken, yüksek alaşımlı beyaz dökme demirlerde 450 – 800 HB gibi bir aralıkta sertlik değerleri elde edilebiliyor. Bu da, üretilen malzemenin çok daha yüksek bir aşınma direnci sergileyebileceği anlamına geliyor.
Yukarıda beyaz dökme demirlerin kısa bir tanımını yaparken, malzemeye sertliğini veren fazın sementit adı verilen demir karbür parçacıkları olduğunu söylemiştik. Bu eksende düşündüğümüzde, beyaz dökme demirin sertliğini daha da arttırmak istediğimizde, daha sert ve daha fazla miktarda karbür parçacıklarına ihtiyaç duyacağımızı anlayabiliyoruz. Bu parçacıkları elde edebilmek için, dökme demir içine krom gibi oldukça kuvvetli karbür yapıcı elementler ekliyoruz. Katılaşma sürecinde oluşan ve hacimsel olarak geniş bir yer kaplayan birincil ve ötektik karbür parçacıkları, dökme demirin çok daha sert bir yapı sergilemesini sağlıyor. Ayrıca malzeme içinde krom bulunması, dökme demirin sertliğini arttırırken, aynı zamanda korozyon direncini de arttıran bir etki ortaya çıkartıyor.
Bu noktada, üretilen bu malzemenin mekanik özelliklerinin sadece karbür parçacıklarına değil, aynı zamanda bu parçacıkları çevreleyen matrise de bağlı olduğunu vurgulamamız lazım. Eğer tüm yapı sadece sert ve aynı zamanda kırılgan bu karbür parçacıklarından oluşsaydı, o zaman ister istemez ürettiğimiz beyaz dökme demirin de oldukça kırılgan bir yapı sergilediğini görürdük. Fakat bu parçacıkları çevreleyen ve metalürji terminolojisinde matris adı verilen faz nispeten sünek bir yapıya sahip olduğu için, ürettiğimiz beyaz dökme demir parçanın sertlik yanında, aynı zamanda belli bir tokluğa da sahip olduğunu görüyoruz. Bu özellik sayesinde kırıcı çene gibi darbeli uygulamalarda, malzemenin kırılmaya karşı bir direnç sergilemesini sağlayabiliyoruz.
Yüksek aşınma direncine sahip bu beyaz dökme demirlerin mekanik değerleri ve kompozisyonları hakkında belirlenen standartlara ulaşmak isteyen okuyucularımızın ASTM A 532 standardından bilgi alabileceklerini hatırlatalım.
Şimdi bu genel girişin ardından, sanayide en sık üretilen iki tür yüksek alaşımlı beyaz dökme demire biraz daha yakından bakalım.
Yüksek kromlu beyaz dökme demirler
Krom, oldukça kuvvetli bir karbür yapıcı element olduğu için, yavaş soğuyan parçalarda bile beyaz dökme demir yapısının ortaya çıkmasını sağlayabiliyor. Diğer bir deyişle, yüksek krom takviyesiye hazırlanan alaşımlarda hızlı soğuma gereksinimi ortadan kalktığı için, 10 ton gibi yüksek ağırlığa sahip parçaların bile, tamamen beyaz yapı sergileyecek şekilde dökülmesini sağlayabiliyoruz. Yapılarında bulunan birincil ve ötektik karbür parçacıkları sayesinde, bu dökme demirlerin oldukça yüksek aşınma direnci sergilediklerini görüyoruz. Eğer sertlik yanında, parçanın tokluğunun da yüksek olması isteniyorsa, o zaman bu parçacıkların hacimsel oranı da önem kazanıyor. Tahmin edebileceğiniz üzere bu parçacıkların hacimsel oranı ile malzemenin tokluğu arasında ters bir ilişki olduğunu görüyoruz. Hacimsel orana ek olarak, karbür parçacıklarının boyut dağılımı, parçacıkların biçimsel özellikleri ve parçacıklar arasındaki ortalama mesafe de, malzemenin tokluğuna etki eden diğer parametreler olarak karşımıza çıkıyor.
Karbür parçacıklarına ek olarak, parçaya ısıl işlem uygulayarak da belli bir miktar tokluk kazanmasını sağlayabiliyoruz. Tabii burada ısıl işlemi karbür parçacıklarının yapısını değiştirmek için değil, karbür parçacıklarını çevreleyen matris yapısı ile oynamak için uyguladığımızı vurgulamamız lazım.
Nikel-kromlu beyaz dökme demirler
Sanayide Ni-hard adıyla da bilinen bu dökme demirler, özellikle kırıcı ve öğütücü parçalarda uzun bir süredir kullanılıyor. Yukarıda bahsettiğimiz karbür yapıcı kroma ek olarak, bu dökme demirler aynı zamanda bir miktar nikel de içeriyorlar. Dökme demir içinde %3 – %5 oranında bulunan nikel, yüksek sıcaklıklık fazı olan östenitin perlite dönüşmesini engelliyor. Bu şekilde, hızlı bir soğutmayla östenit yapısının oldukça sert bir faz olan martensite dönüşmesini sağlayabiliyoruz. Herhangi bir yanlış anlaşılma olmasının önüne geçmek için tekrar vurgulamamızda fayda olabilir: Burada karbür parçacıklarına dair bir dönüşümden değil, karbür parçacıklarını çevreleyen matrisin yapısına dair dönüşümlerden bahsediyoruz.
Yukarıda anlatılanlardan anlaşılabileceği üzere, beyaz dökme demire sertliğini karbür parçacıkları veriyor. Bu karbür parçacıkları da hem demir ve karbon, hem de krom ve karbon arasında oluştuğu için, aşınma direncini arttırmak için %1,5 – %4 arası kroma ek olarak, karbon miktarının da %3,5 civarında tutulması gerekebiliyor. Eğer malzemenin tokluğunun da yüksek olması gerekiyorsa, o zaman karbon miktarını %2,7 civarına çekmek durumunda kalıyoruz.
ASTM A 532 standardına göre dökme demire en fazla %1,3 oranında eklenen mangan, bir yandan perlit oluşumunu engellediği gibi, aynı zamanda östenit stabilize edici bir etki de ortaya çıkartıyor. Bu nedenle manganın nispeten yüksek olması durumunda, ısıl işlem sonrasında yapıda kalıntı östenit miktarının arttığını, buna bağlı olarak sertliğin de nispeten daha düşük seviyelerde kaldığını görüyoruz. Silisyum ise, hem sıvı akışkanlığını arttırdığı, hem de martensit oluşumuna katkıda bulunduğu için, yüksek alaşımlı dökme demirlere %1 ila %1,5 arasında ekleniyor.
Kaynaklar ve ek bilgiler
İçerik hazırlığında kullanılan tüm kaynakların listesi için bu bağlantıyı takip edebilirsiniz.
Yazan: Dr. Arda Çetin. (Dökümhane Akademi ekibi hakkında ayrıntılı bilgi için bu bağlantıyı takip edebilirsiniz.)